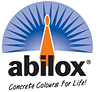

The importance of uniformity of ingredient materials and procedures:
Concrete is a mixture of naturally occurring and manufactured materials of varying colours and characteristics. Therefore, for a given project, raw materials should be obtained from the same source to the same specification without variation. They should be stored for use in such a way as to maintain their complete uniformity when batching concrete. Consistency and uniformity of all procedures and processes is also essential. Whatever the materials, their proportions and the methods or timing of procedures used in the manufacture of through-coloured concrete for uniform results they are to be precisely the same.
Every step carried out in the same way from pour to pour, pavement to pavement, area to area, panel to panel, column to column etc. will assist in achieving uniform (and permanent) colouration of the concrete using suitable pigments such as the abilox® range of mineral oxides. Following are a few recommendations to assist in achieving the uniformity of colour results that many specifiers require:
Cement:
The colour of a particular brand and type of cement affects the final colour of a particular grade and class of pre-mixed concrete. The use of an off-white cement will result in a different colour in a given concrete mix design to that obtained with a grey cement - with or without the incorporation of mineral oxide colouring pigments. Whatever the cement colour chosen, it is wise to ensure that it comes from a single source of manufacture. The colour of one manufacturer's cement type usually differs from another's.
Thorough pigment mixing requirements:
To obtain colour uniformity and maximum intensity of colour related to the dose rate, the oxide pigment powder must be thoroughly dispersed throughout the concrete batch. Many concrete technologists believe that it takes at least 8 minutes mixing time at the fastest barrel speed for any admixture to be uniformly dispersed homogeneously throughout a barrel load of freshly prepared plastic concrete in a premixed concrete transit truck.
Therefore, concrete containing a typically normal amount of 20mm coarse aggregate, a uniform mixing time of ten (10) minutes at the fastest barrel speed is recommended when through (integrally) coloured concrete using suitable colouring pigments is being prepared and supplied by this means. From all points of view, it is important to specify a uniform, and in terms of time an adequate mixing regime for the pigmentation of concrete whether carried out on site or at a premixed concrete supplier's batching plant.
Water to cementitious ratio:
Most people concerned with building and construction are aware that amongst other factors, the hardness, mechanical strengths, shrinkage and cracking resistance as well as the durability of concrete is greatly and beneficially influenced when the amount of water compared to that of the cement or cementitious binder is kept relatively low. The lower the water to cementitious material ratio (w/c ratio), the higher the performance.
However, it appears that when making through-coloured concrete with the use of suitable colouring pigments, many people are unaware that achieving low water to cementitious binder ratios, usually by means of a suitable admixture, also increases the colour intensity of colouring pigments at a given pigment dose rate.
In a given concrete mix design, a high water content compared with a low one, makes a greater volume of cement paste 'glue'. At a given pigment dose rate weight, the intensity of colour of the concrete is weakened as a result - as is its mechanical strengths, ie it may be considered that the intensity of pigmentation as well as the concrete's performance are adversely affected. When strong intense colours are required, the decision may be made at a slightly higher cost to keep the w/c ratio of the concrete at a uniformly low level whilst maintaining a suitable liquid consistency or slump for forming, pumping, placement, finishing, etc by means of the addition of a suitable super water reducing and/or superplasticising admixture*.
Avoiding colour problems with form-work:
Water absorption:
Avoid varying the forming material. Different formwork materials may have different rates and characteristics of water absorption. These may affect cement hydration and its colour at the concrete's surface. Impervious forms such as polyurethane or steel will behave differently to timber. Although plywood and Oregon are both porous timbers, they will, due to their different densities, behave differently. New and used timber formwork should be pre-conditioned to make their surfaces uniform or mortar/concrete applied, allowed to set and then cleaned off prior to use to minimise the probability of colour variation at the concrete's off-form surface.
Surface temperature:
The heat of hydration of concrete at a form's surface may vary with different forming materials - timber, polyurethane, fibreglass or steel - resulting in potential colour variation - even with unpigmented concrete.
Stripping time of precast concrete:
The time concrete spends in the form after setting affects hydration. To minimise colour variations, the interval between the setting of the concrete and the stripping of the formwork (or form liner) should be consistent. In addition to the factors previously mentioned, it appears that the uniformity of colour of pigmented concrete is proportional to an adequate time concrete is left in its mould or formwork before stripping the formwork or demoulding the concrete unit. 'Weekend' precast concrete usually results in units having ideal colour uniformity but they may not match 'weekday' units. Therefore, despite a higher cost to make them uniform, it may be beneficial to leave precast concrete units in their moulds for say 36 instead of 18 hours. The increased time concrete spends in the form or mould affects hydration (it is being cured) and colour uniformity. To minimise colour variation, the interval between the placement of the concrete and the stripping of the formwork / formliner should be adequate as well as consistent from one panel and the next.
* In addition to that range of 60 UV resistant abilox® mineral oxide colouring pigment powders, Ability offers its Efflorein® Mark 2 and Cosmotron® DPU-AC instantly dispersing, high purity powder admixtures for concrete - both of which are often used in combination, but added separately to a batch of concrete after suitable testing and trials in a given concrete mix design.
The procedure of curing:
Curing - the important procedure of preventing the evaporation of the mixing water used to make concrete - to be adopted immediately after it sets (example: at 23°C for N32 grade concrete - immediately after 4 hours has elapsed after mixing!)
Most people concerned with good building and construction practices are aware that not adopting a suitable curing procedure - especially under adverse hot/windy weather conditions - can result in up to 50% of the mechanical strengths of a particular grade of concrete being lost ie: N40 grade concrete (40MPa compressive strength at 28 days) can be reduced to N32 (32MPa compressive strength). The importance of adopting a suitable curing regime can therefore not be over-emphasised.
The procedure of curing carried out uniformly and continuously is also beneficial to the achievement of uniform, integrally coloured concrete. Ability offers its Duro-Seel Clear liquid coating product for the procedure of curing.
It is a dual-use product as it is used as:
(i) a membrane curing compound or 'same day' sealer for freshly placed concrete.
(ii) as a long-life sealer coating for existing concrete.
Rate of hardening varies according to concrete temperature:
The mechanical strengths of various grades/classes of pre-mixed concrete at a given, unchanged temperature and different ages will vary. These mechanical strengths (although increasing with time) at different ages will also vary for a particular grade or class of concrete according to the variation in diurnal (day to night to day) temperatures.
For example, most grades of concrete only reach, with satisfactory curing, about 26% of their ultimate mechanical strengths at a non-varying temperature of 23°C and satisfactory curing over 24 hours ie under concrete laboratory conditions. This strength gain percentage is reduced over the same period of time if the external ambient temperature drops, as it usually does during the night.
For uniformly coloured concrete using pigments it is recommended that, at higher cost, concrete is allowed to reach at least 40% of its ultimate mechanical strengths before lifting from moulds and then the immediate re-commencement of a suitable curing regime such as continuous water spray curing be carried out for all concrete surfaces thus exposed to the air. The use of a super plasticising admixture can substantially assist in attaining this rule of thumb figure of 40% of the ultimate mechanical strengths in the shortest time at the lowest temperatures.
Conclusion:
With a little pre-planning and care taken to ensure complete uniformity of manufacture, the achievement of uniform colour effects in pigmented integrally coloured in situ and precast concrete is relatively easy. The uniformity of other manufactured pigmented materials, such as paints, inks, plastics, resins - for example epoxies, rubbers and other composite materials - is achieved with these same principles
|